Introduction:
In the world of industrial applications and emergency power backup systems, diesel generators play a critical role in ensuring uninterrupted power supply. One of the key functions of diesel generators is motor starting, which is essential for various industries such as manufacturing, construction, mining, and marine operations. In this comprehensive guide, we will explore the importance of diesel generators for motor starting, their working principles, key components, selection criteria, and maintenance practices.
Importance of Diesel Generators for Motor Starting:
Motor starting is a crucial operation in many industrial processes where heavy-duty machinery and equipment are used. These motors often require a high starting current to overcome inertia and bring the equipment up to operating speed. Diesel generators are well-suited for this task due to their ability to provide high starting currents and maintain stable power output during the transient phase of motor starting.
In industrial applications, sudden power interruptions can lead to significant downtime, loss of productivity, and potential damage to equipment. Diesel generators act as a reliable source of backup power, ensuring that critical motors can be started promptly in the event of a power outage. The robust and dependable nature of diesel generators makes them ideal for powering motors in challenging environments where grid power may be unreliable or unavailable.
Working Principles of Diesel Generators for Motor Starting:
Diesel generators operate on the principle of converting chemical energy stored in diesel fuel into mechanical energy through combustion. The basic components of a diesel generator include an engine, alternator, fuel system, cooling system, exhaust system, and control panel. During motor starting, the diesel generator's engine is started using an electric starter motor or manual crank. Once the engine reaches the required speed, the alternator generates electrical power, which is then supplied to the motor through the switchgear system.
The key factor that makes diesel generators suitable for motor starting is their ability to provide high starting torque and current. The diesel engine's high compression ratio and robust construction allow it to deliver sufficient power to overcome the inertia of the motor and bring it up to speed. Additionally, diesel generators can maintain stable voltage and frequency output, ensuring that the motor operates smoothly without any fluctuations or interruptions.
Components of Diesel Generators for Motor Starting:
1. Engine: The heart of a diesel generator, the engine converts the energy stored in diesel fuel into mechanical power. Diesel engines are known for their durability, efficiency, and high torque output, making them ideal for powering heavy-duty motors during starting operations.
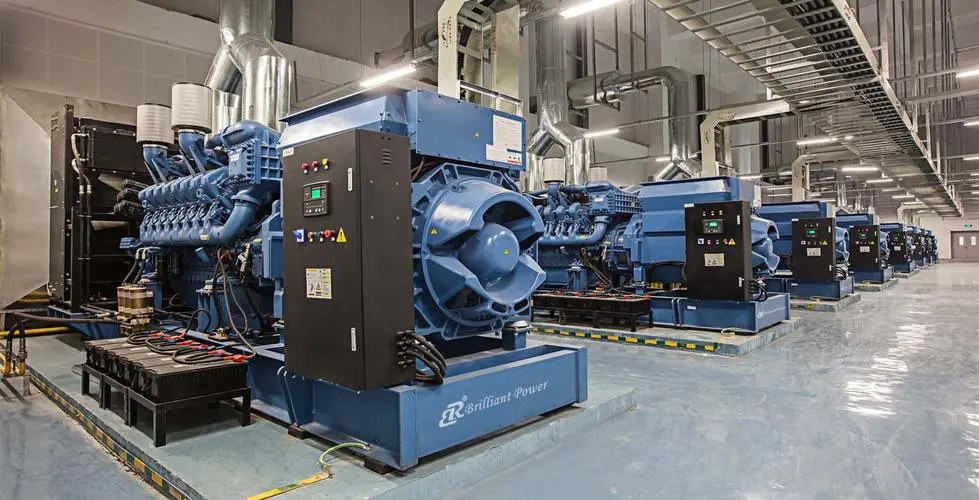
2. Alternator: The alternator is responsible for converting mechanical power from the engine into electrical power. It generates the voltage and frequency required to start and operate the motor efficiently.
3. Fuel System: The fuel system supplies diesel fuel to the engine for combustion. It consists of fuel tanks, filters, pumps, and injectors that ensure the proper delivery of fuel to the engine for optimal performance.
4. Cooling System: Diesel engines generate a significant amount of heat during operation, necessitating a cooling system to maintain optimal operating temperatures. Cooling systems typically include radiators, fans, and coolant circulation components to prevent overheating.
5. Exhaust System: The exhaust system removes combustion gases and emissions from the engine and directs them out of the generator. Proper exhaust design is essential for maintaining air quality and complying with environmental regulations.
6. Control Panel: The control panel houses the electrical components and controls of the diesel generator, allowing operators to start, stop, and monitor the generator's performance. It also includes safety features such as overload protection, voltage regulation, and engine diagnostics.
Selection Criteria for Diesel Generators for Motor Starting:
When choosing a diesel generator for motor starting applications, several factors must be considered to ensure optimal performance and reliability:
1. Power Output: The generator should have sufficient power output to meet the starting requirements of the motor it will be powering. It is essential to calculate the starting current and torque of the motor to determine the appropriate generator size.
2. Voltage and Frequency Regulation: The generator should provide stable voltage and frequency output to ensure the motor operates within its rated parameters. Voltage and frequency fluctuations can lead to motor damage and performance issues.
3. Engine Type and Size: The engine's horsepower, torque, and starting capabilities should match the motor's requirements. Diesel engines are available in various sizes and configurations, so it is essential to select the right engine type for the application.
4. Fuel Efficiency: Diesel generators should be fuel-efficient to minimize operating costs and reduce environmental impact. High-efficiency engines and advanced fuel injection systems can help optimize fuel consumption.
5. Durability and Reliability: Diesel generators should be built with robust materials and components to withstand harsh operating conditions and provide reliable performance over the long term. Quality construction and reputable brands are essential considerations.
6. Maintenance Requirements: Regular maintenance is crucial for ensuring the optimal performance and longevity of diesel generators. Consider the maintenance schedule, serviceability, and availability of spare parts when selecting a generator for motor starting applications.
150kw diesel generator for remote locations for Diesel Generators for Motor Starting:
Proper maintenance is essential to keep diesel generators in optimal condition and ensure reliable performance during motor starting operations. Here are some key maintenance practices for diesel generators:
1. Regular Inspections: Conduct routine visual inspections of the generator components, including the engine, alternator, fuel system, cooling system, and electrical connections. Look for signs of wear, leaks, or damage that may indicate potential issues.
2. Oil and Filter Changes: Follow the manufacturer's recommendations for oil and filter changes to maintain proper lubrication and engine performance. Regular oil analysis can help identify any internal engine problems early.
3. Cooling System Maintenance: Keep the cooling system clean and free of debris to prevent overheating. Check coolant levels, inspect hoses and connections, and replace coolant as needed to ensure effective heat dissipation.
4. Fuel System Maintenance: Monitor fuel quality, replace fuel filters regularly, and ensure proper fuel storage to prevent contamination and fuel system issues. Clean fuel tanks and lines to prevent clogs and fuel supply interruptions.
5. Battery Maintenance: Check battery condition, terminals, and connections regularly to ensure proper starting power. Clean terminals, test battery voltage, and replace weak batteries to prevent starting failures.
6. Load Testing: Periodically conduct load tests on the generator to simulate motor starting conditions and verify its ability to handle peak loads. Load testing can identify potential issues and ensure the generator's readiness for critical operations.
Conclusion:
Diesel generators play a vital role in motor starting applications across various industries, providing reliable backup power and ensuring uninterrupted operations. The high starting torque, stable output, and robust construction of diesel generators make them well-suited for powering heavy-duty motors in challenging environments. By understanding the working principles, components, selection criteria, and maintenance practices of diesel generators for motor starting, operators can optimize their performance and enhance system reliability. Investing in quality diesel generators and implementing proper maintenance procedures will help minimize downtime, improve productivity, and safeguard critical equipment in industrial settings.